Packaging
Packaging Solutions with Variable Frequency Drives (VFDs)
Introduction
Variable Frequency Drives (VFDs) are electronic devices used to control the speed and torque of electric motors. In packaging solutions, VFDs play a crucial role in enhancing efficiency, precision, and flexibility of various packaging processes.
Benefits of VFDs in Packaging
- Energy Efficiency: VFDs help reduce energy consumption by adjusting the motor speed to match the load requirements. This leads to significant energy savings, especially in applications with variable loads.
- Improved Process Control: VFDs allow for precise control of motor speed and torque, which is essential for maintaining consistent quality in packaging processes. This results in reduced waste and higher product quality.
- Extended Equipment Life: By reducing the mechanical and electrical stress on motors, VFDs help extend the lifespan of the equipment. Smooth start and stop operations prevent sudden jerks and mechanical wear.
- Flexibility: VFDs provide flexibility in packaging lines by allowing quick adjustments to different packaging speeds and requirements. This is particularly beneficial in multi-product packaging lines.
- Reduced Maintenance Costs: VFDs can monitor motor performance and predict maintenance needs, thereby reducing downtime and maintenance costs.
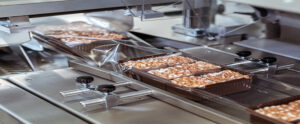
Applications in Packaging Solutions
- Conveyor Systems: VFDs control the speed of conveyor belts, ensuring smooth and efficient movement of products through the packaging line. They can adjust speeds for different packaging stages and synchronize multiple conveyors.
- Pumping Systems: In liquid packaging, VFDs regulate pump speeds to ensure accurate filling levels, reducing spillage and waste.
- Compressors and Blowers: VFDs manage the speed of compressors and blowers used in packaging processes such as sealing, vacuum packaging, and air-filled cushioning.
- Labeling and Printing: VFDs provide precise control over the speed of labeling and printing machines, ensuring accurate placement and high-quality printing on packages.
- Sorting and Indexing: VFDs enhance the accuracy and speed of sorting and indexing systems, which are critical for high-speed packaging lines.
Choosing the Right VFD
When selecting a VFD for packaging solutions, consider the following factors:
- Motor Compatibility: Ensure the VFD is compatible with the type of motor used in the packaging equipment.
- Load Requirements: Choose a VFD that can handle the load requirements of the application, including peak loads.
- Control Features: Look for advanced control features such as torque control, speed control, and multi-motor control.
- Environment: Consider the operating environment, including temperature, humidity, and exposure to dust or chemicals. Select a VFD with appropriate protection ratings.
- Connectivity: Ensure the VFD can integrate with existing control systems and has capabilities for remote monitoring and diagnostics.
Implementation Considerations
- Proper Sizing: Correctly size the VFD to match the motor and application requirements to avoid overloading or underutilization.
- Harmonics and Interference: Address potential issues related to harmonics and electromagnetic interference (EMI) by using filters and shielding as needed.
- Cooling and Ventilation: Ensure adequate cooling and ventilation for the VFD to prevent overheating and ensure reliable operation.
- Training and Support: Provide training for operators and maintenance personnel on VFD operation, troubleshooting, and maintenance.
Conclusion
VFDs offer numerous benefits for packaging solutions, including energy efficiency, improved process control, and reduced maintenance costs. By carefully selecting and implementing VFDs, packaging operations can achieve greater flexibility, reliability, and overall performance.